Measuring the geometry of pins optically in 3D
Frank Uibel, a long-time expert in the field of press-fit technology and active member of the IPC, recommends Bruker Alicona technology as a "fast, simple and accurate measuring tool" for the geometric verification of press-fit zones. We wanted to know why and asked him these questions.
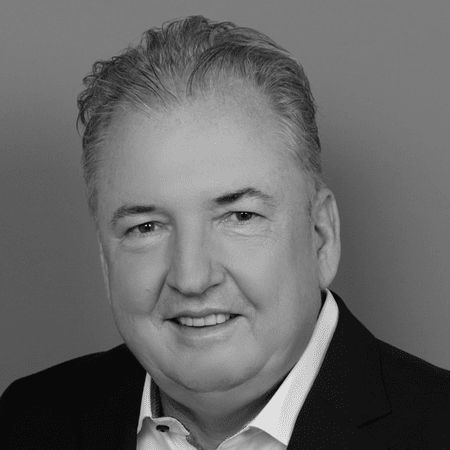
Frank Uibel
Owner of Uibel Consulting
Expert in the field of press-fit technology and active member of the IPCBruker Alicona technology is characterized by fast measurement times, easy handling and high accuracy.
READ THE ENTIRE SUCCESS STORY
What is measured?
Press-fit technology is a special connection technique used to create solderless electrical connections. Contact parts or entire components with press-fit zones are pressed into metallized holes in a printed circuit board. This creates a stable, gas-tight and highly conductive connection between the press-fit zone and the hole wall. There are currently a number of different press-fit zones available that have one thing in common: The geometry is one of the decisive factors for a good connection. From a metrology point of view, the geometry poses a number of challenges. These include the measurement of edge radii, enveloping circles at certain positions or transitions such as that from the press-fit zone to the press-fit tip. Measurements must be available with the necessary accuracy, while at the same time a high measuring speed and documentation of the results are required.
How Uibel succeeds with Bruker Alicona solution
InfiniteFocusSL
3D measurement system for form & finish
- Easy, fast and traceable measurement of form and finish on micro structured surfaces
- Users measure both form and roughness of components with only one system
- With an automation interface, InfiniteFocusSL is also applied for fully automatic measurement in production