Optische Messtechnik integriert in eine Fertigungszelle
KLEINER Stanztechnik kombiniert in einer neuen Fertigungszelle Werkzeugmaschinen, Messtechnik und Robotik. Ziel ist die autarke, vollautomatische Fertigung von Werkzeugkomponenten inklusive Messprotokoll. Alicona ist nicht nur wegen seiner Automatisierungsmöglichkeiten ausgewählter Messtechnik-Partner.
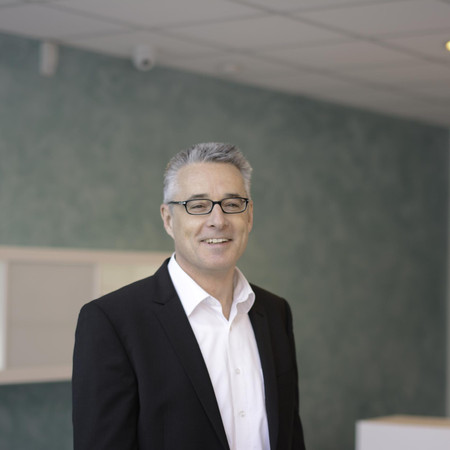
Christian Hamann
Geschäftsfeldleiter Werkzeugtechnik bei KLEINER Stanztechnik
Mit Bruker Alicona sind wir bereits in der Lage, den Messvorgang in unserem Produktionsprozess automatisch zu starten und durchzuführen. Derzeit arbeiten wir daran, die Vernetzung mit anderen Maschinen zu ermöglichen, so dass die Maschinenparameter automatisch und kontinuierlich auf der Grundlage der Messergebnisse angepasst werden.
Bruker Alicona Messsystem bei Kleiner 2.0 - sehen Sie in diesem Video, wie Kleiner das optische Koordinatenmessgerät µCMM mit einer hochpräzisen Rotationseinheit direkt in die Fertigungszelle integriert.
LESEN SIE DIE GESAMTE ERFOLGSGESCHICHTE
Optische 3D-Messung kombiniert mit Werkzeug-, Formenbau- und Industrierobotertechnologien
Christian Hamann, Geschäftsfeldleiter Werkzeugtechnik bei KLEINER Stanztechnik, bleibt bescheiden: "Ob wir mit unserer neuen Fertigungszelle weltweit alleinstehend sind, kann ich nicht so ohne Weiteres sagen. Doch unsere Kunden bestätigen, dass sie eine vergleichbare Fertigungszelle mit integrierter Messtechnik und diesem hohen Automatisierungsgrad noch nicht gesehen haben." Das Stanztechnikunternehmen aus Pforzheim ist stolz darauf, seit seiner Gründung Kompetenzen aus dem Bereich Präzisionsstanzteile und Hochleistungsstanzwerkzeuge mit neuen Technologien zu kombinieren und damit steigenden Kundenansprüchen aus unterschiedlichen Industrien gerecht zu werden.
Mit seiner neuen Fertigungszelle, die Technologien aus dem Werkzeug- und Formenbau, der Messtechnik und Industrierobotik miteinander verbindet, stellt KLEINER seine Innovationskraft einmal mehr unter Beweis. Für Christian Hamann ist die Inbetriebnahme ein Meilenstein: "Im Moment interagieren Mensch und die einzelnen Komponenten der Zelle noch miteinander. Die Fertigungszelle in ihrem finalen Zustand wird eine völlig autarke Fertigung mit vollautomatischem Ablauf ermöglichen. Wir übergeben der Zelle einen Rohling, und am Ende erhalten wir ohne weiteren Eingriff ein komplett gefertigtes Werkzeug inklusive Messprotokoll."
Wie Kleiner mit der Bruker Alicona-Lösung erfolgreich ist

InfiniteFocus
Form- und Rauheitsmessgerät
- Genaues, schnelles und universelles optisches 3D-Messgerät für Toleranzen im µm- und sub-µm-Bereich
- Bauteile werden unabhängig von Größe, Material, Geometrie, Gewicht & Oberflächenbearbeitung flächenbasiert und hochauflösend gemessen
- Eine Reihe von bewährten und neuen Features kombinieren die Funktionalitäten eines Rauheitsmessgeräts (Ra, Rq, Rz/Sa, Sq, Sz) mit denen einer Koordinatenmessmaschine